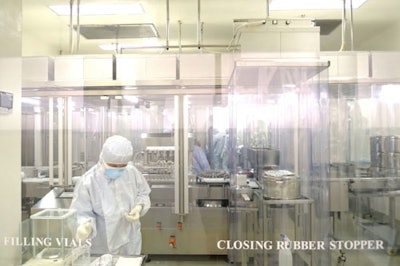
It is no secret that our readers who manage pharmaceutical packaging operations often lag behind their brethren in food, beverage, or even personal care, as measured by Overall Equipment Effectiveness (OEE), for instance.
While many industries like oil and gas, wastewater, and food/beverage, have adopted continuous manufacturing processes to achieve greater efficiency, pharmaceutical operations lag behind here as well.
But continuous drug manufacturing could be on the horizon, a mere five or 10 years away, according to comments on the Web site PharmaQbD (quality by design). Senior Editor Paul Thomas reports on a recent annual meeting of the American Assn. of Pharmaceutical Scientists held in New Orleans last November, focusing on a half-day symposium, “Continuous Manufacturing: Benefits and Challenges.”
According to Thomas' report, the U.S. Food and Drug Administration is in full support of drug manufacturers who wish to adopt continuous manufacturing methods. The agency understands both the quality and economic benefits of continuous processes, and acknowledges that the science already exists and is being implemented in other industries.
While there are “no regulatory hurdles,” the FDA admits a lack of experience both at the agency and with the manufacturers and cautions for early and frequent conversations.
James Evans, PhD, Associate Director of the Novartis-MIT Center for Continuous Manufacturing, hopes drug manufacturing with continuous processes can be “a rock star” for pharma. According to the PharmaQbD report, Evans contends continuous processes could make drug manufacturing more economically viable and sustainable, be cleaner, leaner and more energy efficient, and could even leverage new chemistries.
Evans painted a “blue sky” vision of continuous manufacturing from synthesis through tableting and packaging, that could potentially deliver product to a patient in 10 days (versus current-day models of between 100 to 300 days) but implementation calls for new facility layouts, new product development processes, and “major changes” in the technical skills of the engineers.
“We need to transform the operator,” says Evans. “The system is highly automated and requires a high-skilled operator who understands the entire process.”
Evans calls on players from across the entire industry, from pharmaceutical companies and process automation and software vendors to universities and analytical and process equipment makers, to spread the value proposition, and to embed continuous processes into product development as early as possible.
While many industries like oil and gas, wastewater, and food/beverage, have adopted continuous manufacturing processes to achieve greater efficiency, pharmaceutical operations lag behind here as well.
But continuous drug manufacturing could be on the horizon, a mere five or 10 years away, according to comments on the Web site PharmaQbD (quality by design). Senior Editor Paul Thomas reports on a recent annual meeting of the American Assn. of Pharmaceutical Scientists held in New Orleans last November, focusing on a half-day symposium, “Continuous Manufacturing: Benefits and Challenges.”
According to Thomas' report, the U.S. Food and Drug Administration is in full support of drug manufacturers who wish to adopt continuous manufacturing methods. The agency understands both the quality and economic benefits of continuous processes, and acknowledges that the science already exists and is being implemented in other industries.
While there are “no regulatory hurdles,” the FDA admits a lack of experience both at the agency and with the manufacturers and cautions for early and frequent conversations.
James Evans, PhD, Associate Director of the Novartis-MIT Center for Continuous Manufacturing, hopes drug manufacturing with continuous processes can be “a rock star” for pharma. According to the PharmaQbD report, Evans contends continuous processes could make drug manufacturing more economically viable and sustainable, be cleaner, leaner and more energy efficient, and could even leverage new chemistries.
Evans painted a “blue sky” vision of continuous manufacturing from synthesis through tableting and packaging, that could potentially deliver product to a patient in 10 days (versus current-day models of between 100 to 300 days) but implementation calls for new facility layouts, new product development processes, and “major changes” in the technical skills of the engineers.
“We need to transform the operator,” says Evans. “The system is highly automated and requires a high-skilled operator who understands the entire process.”
Evans calls on players from across the entire industry, from pharmaceutical companies and process automation and software vendors to universities and analytical and process equipment makers, to spread the value proposition, and to embed continuous processes into product development as early as possible.