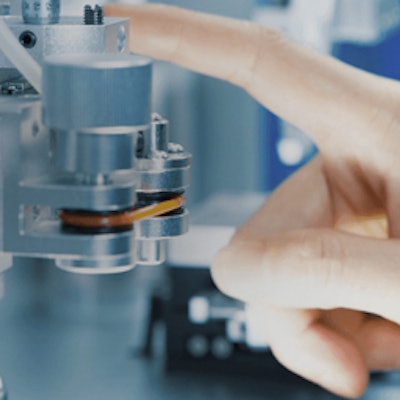
When INEOS Barex® AG announced in 2014 that it intended to close the Barex® plant in Lima, OH—the sole facility producing it—the worldwide pharmaceutical industry faced the loss of a staple barrier film. The plant closed in the first quarter of 2015.
Several plastics and packaging companies are working to find alternatives and were exhibiting their progress at Pharma EXPO 2015. For instance, Bemis is testing alternatives to Barex for the sealant layer in transdermal patch constructions.
Bemis has introduced PerfecPharmTM P616 (CXB™ Sealant), a blown modified ethylene co-polymer film, and PerfecPharm™ P619 (PET Sealant), an amorphous polyethylene terephthalate cast sealant. In addition to meeting common barrier property requirements for transdermal packaging, these Bemis specifications exhibit low permeation and absorption characteristics.
Flex-pack supplier Rollprint exhibited Exponent2, a high-barrier, peelable film that can function as an alternative to Barex. These extrusion-coated sealants provide excellent water vapor and oxygen barrier. Available in both peelable and weld seal versions, Exponent provides high-barrier clear film options where previous package choices were limited to aluminum foil laminations or glass. Exponent materials are for pharmaceuticals, including transdermal patch and single-dose delivery systems.
Why the emphasis on replacing Barex? Global transdermal patch delivery of drugs is a $25 billion market (2014) and is on its way to being a $40 billion market (2018), according to Bemis, with some 90 drugs in the pipeline that will utilize patches. So it’s well worth finding effective and readily available alternatives to Barex.
Testing methodology
In their presentation entitled, "Materials Science: Case Study for Rational Design of Transdermal Patch Packaging," Rishabh Jain and Yuan Liu, Research Scientists, took the Innovation Stage during Pharma EXPO to present the results of their testing of these two alternatives to Barex. The testing examined chemical resistance, diffusion barrier performance, and ability to resist delamination. The two scientists also explained the methodology used to understand permeability of the drugs into the sealant layer.
According to the speakers, packaging of transdermal patches requires the package sealant to be impermeable to the transdermal Active Pharmaceutical Ingredient (API), that it prevent loss of the API, and that it preserve the structural integrity of the packaging structure (no delamination).
Since permeability is a function of solubility and diffusivity, the Bemis scientists reasoned that they need ways to test each. Solubility can be modeled using solubility parameters, and diffusivity can be visualized using Raman Imaging. The results can then be confirmed with drug uptake measurements using analytical methods.