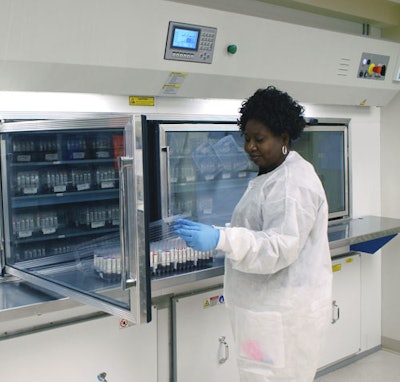
This content was written and submitted by the supplier. It has only been modified to comply with this publication’s space and style.
Prior to the consolidation, regional testing was conducted in four separate facilities causing duplicate supply orders and because storage and retrieval of all items was done manually, items were sometimes stored incorrectly. The traditional rack and shelving system used in the laboratory locations required a large amount of floor space.
"When we consolidated the laboratory operations, we looked for ways to improve the use and efficiency of the space we needed for storage. A primary goal was to keep the costs of constructing the new facility as low as possible," said Jane Lewis, Kaiser Permanente Regional Lab Senior Operations Manager.
Kaiser Permanente chose KardexRemstar vertical carousel storage and retrieval systems and FastPic inventory management and control software to help improve space efficiency at the new laboratory. A refrigerated KardexRemstar vertical carousel is used to store reagents used in testing operations at an optimum temperature. It is installed beside three KardexRemstar Shuttle Vertical Lift Modules (VLMs) used to store laboratory supplies such as gloves, masks and lab coats. The three KardexRemstar Shuttle VLMs that store laboratory supplies replaced shelving that occupied about 2,500 square feet of floor space. The reagent materials were originally stored in 27 36" wide x 26" deep standard refrigerators, occupying some 175 square feet of floor space. Combined, the refrigerated vertical carousel and three Shuttle VLMs occupy only about 712 square feet, a space savings of 74%. By eliminating the standard refrigerators used to store reagent materials, the company also reduced energy consumption and helped improve overall retrieval efficiency.
Efficient Operations
With the former system the laboratory occasionally experienced some difficulty with rotating, resulting in items not being retrieved until after their expiration date. By law, dated materials used in testing operations must be used prior to their expiration date or they must be discarded.
"The installation of the KardexRemstar systems, together with FastPic inventory management software, solved those problems for us," said Erwin J. Cabling, Materials Coordinator. "Now, we don't need to rotate stock. The software directs the vertical storage and retrieval systems to the location of the earliest to expire item and pick lights direct the technician to the specific item."
The KardexRemstar system has reduced the number of supplies contained in the laboratory's inventory, as well. The technical staff keeps a week's worth of supplies near their workbenches. Once per week, the staff provides a list of needed supplies to the materials coordinator who fills the order within 24 hours.
"The FastPic software lets us establish par levels of items so that we don't have to keep track of each individual item in the system," said Mr. Cabling. "We produce a reorder report once per week. We know exactly how much or how many of specific items we have remaining, and what we need to reorder using the software's cycle count reporting feature. "
Mr. Cabling also receives a software generated expiration date report that indicates items set to expire in 30, 60 and 90 days. "Using this report, I'm able to order ahead of time those items due to expire first, and this saves money and time," he said.
Restocking the system is simple. Employees tell the system, through the software, what they're restocking and the automated system retrieves the proper shelf location for that item. In the case of a new lot that has a new expiration number, the system will present a different shelf for storage or the item. That way, materials are always used prior to their expiration date.
"When we consolidated the laboratory operations, we looked for ways to improve the use and efficiency of the space we needed for storage. A primary goal was to keep the costs of constructing the new facility as low as possible," said Jane Lewis, Kaiser Permanente Regional Lab Senior Operations Manager.
Kaiser Permanente chose KardexRemstar vertical carousel storage and retrieval systems and FastPic inventory management and control software to help improve space efficiency at the new laboratory. A refrigerated KardexRemstar vertical carousel is used to store reagents used in testing operations at an optimum temperature. It is installed beside three KardexRemstar Shuttle Vertical Lift Modules (VLMs) used to store laboratory supplies such as gloves, masks and lab coats. The three KardexRemstar Shuttle VLMs that store laboratory supplies replaced shelving that occupied about 2,500 square feet of floor space. The reagent materials were originally stored in 27 36" wide x 26" deep standard refrigerators, occupying some 175 square feet of floor space. Combined, the refrigerated vertical carousel and three Shuttle VLMs occupy only about 712 square feet, a space savings of 74%. By eliminating the standard refrigerators used to store reagent materials, the company also reduced energy consumption and helped improve overall retrieval efficiency.
Efficient Operations
With the former system the laboratory occasionally experienced some difficulty with rotating, resulting in items not being retrieved until after their expiration date. By law, dated materials used in testing operations must be used prior to their expiration date or they must be discarded.
"The installation of the KardexRemstar systems, together with FastPic inventory management software, solved those problems for us," said Erwin J. Cabling, Materials Coordinator. "Now, we don't need to rotate stock. The software directs the vertical storage and retrieval systems to the location of the earliest to expire item and pick lights direct the technician to the specific item."
The KardexRemstar system has reduced the number of supplies contained in the laboratory's inventory, as well. The technical staff keeps a week's worth of supplies near their workbenches. Once per week, the staff provides a list of needed supplies to the materials coordinator who fills the order within 24 hours.
"The FastPic software lets us establish par levels of items so that we don't have to keep track of each individual item in the system," said Mr. Cabling. "We produce a reorder report once per week. We know exactly how much or how many of specific items we have remaining, and what we need to reorder using the software's cycle count reporting feature. "
Mr. Cabling also receives a software generated expiration date report that indicates items set to expire in 30, 60 and 90 days. "Using this report, I'm able to order ahead of time those items due to expire first, and this saves money and time," he said.
Restocking the system is simple. Employees tell the system, through the software, what they're restocking and the automated system retrieves the proper shelf location for that item. In the case of a new lot that has a new expiration number, the system will present a different shelf for storage or the item. That way, materials are always used prior to their expiration date.
Companies in this article