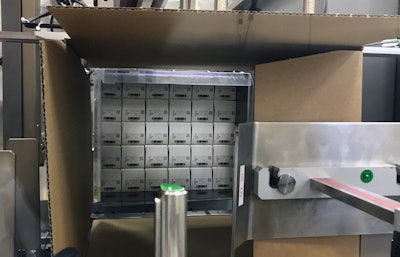
Paris-based Sanofi-aventis S.p.A. installed a new stick-pack line in Q1 of 2019 in its Origgio, Italy, facility just outside of Milan. Both Maalox antacids and Doliprane analgesics are produced on the new line.Maalox 20-count carton.
Essentially a turnkey line from Marchesini, the new line is capable of 800 stick packs/min. That’s twice the capacity of the stick pack line occupying the plant since 2008. This higher throughput is possible because not one but two Marchesini MSP560L filling machines sit at the head of the line. Each takes a 600-mm-wide roll-fed lamination of polyester/foil/polyethylene, forms it into tubes 10-across, fills the required amount of liquid, and seals stick packs in any one of four sizes: 4.3, 10-, 8.3-, or 12.5-mL. Shelf life on the finished pack is two to three years, depending on which product and, to some extent, which region of the world it goes to.
Featuring a small footprint relative to comparable systems, the MSP560L also has a greatly streamlined and software-based Clean-In-Place function that saves a lot of time when Sanofi switches from one liquid product to another. It also has a roll-fed film infeed system that has been simplified, says Marchesini, so that the operator can change the roll quickly and easily. The front of the machine allows easy access to the working parts, which means the operator has a clear and direct view of the entire packaging process. An automatic roll-centering device guarantees that the material is always correctly aligned with machine operations. As for date coding, each MSP560 has two Videojet 3340 laser coders that mark all 10 lanes of packaging material. Paired with the laser coders is a vision inspection system from SEAVision that verifies accuracy and legibility of the printed data. Two of these stick pack fillers sit at the head of the line. Visible on the far right is the robotic transfer unit that takes filled stick packs out of their shuttles and sends them through a 90-deg turn toward the cartoner.
According to Luca Angelini, Technical Services and Information Systems Manager at the Sanofi plant, his firm’s long-standing relationship with Marchesini made them an obvious choice when it came time to pick a machine supplier. But what really sealed the deal was their ability to design a dual-filler line. Each filler—producing stickpacks 10-across, or 10 per cycle—is capable of 400 three-side-sealed stick packs/min, so the combined output is 800/min. Should one filler be in need of service or maintenance, the other one is perfectly happy to operate alone. But if both are running simultaneously, which is usually the case, it means the downstream packaging systems had better be optimally efficient in their collating, cartoning, date coding, case packing, and palletizing functions. And boy are they.
Innovative transfer concept
Perhaps most notable where secondary packaging is concerned is the use of intermittent-motion shuttles—one dedicated to each stick pack machine—and robotic pick-and-place units that smoothly transfer the stickpacks from the two machines that make them and send them into a 90-deg turn leading into the cartoning machine downstream. Mounted on a long elliptical shaped track, each shuttle holds 20 slots. The shuttle pauses beneath an MSP560L so that 10 stick packs can drop into the front 10 slots. The shuttle then advances a short distance to the second MSP560L machine so that 10 more stick packs can drop into the trailing 10 slots. Once all 20 slots contain a stick pack, the shuttle advances a short distance and pauses beneath a robotic pick-and-place unit that uses vacuum pickup cups to pick all 20 stick packs from their slots. The robot strokes forward while its end effector pivots 90 deg and drops all 20 stick packs into a continuous-motion flighted takeaway conveyor. In this way, the stick packs execute the 90-deg turn that takes them into the cartoning, case packing, and palletizing equipment downstream. As for the track-mounted shuttle, as soon as it has delivered its load of 20 stick packs to the robotic pick-and-place unit, it proceeds along the bottom half of its elliptical track until it arrives back at the two MSP560L machines to receive another 20 stick packs.A robotic device picks 20 stick packs from a shuttle (A) and, after turning them 90 deg, places them into a flighted takeaway conveyor (B). A short distance downstream, a second robotic pick-and-place unit (C) picks stick packs from the flighted takeaway conveyor and places them in a bucket conveyor that leads to the cartoner.