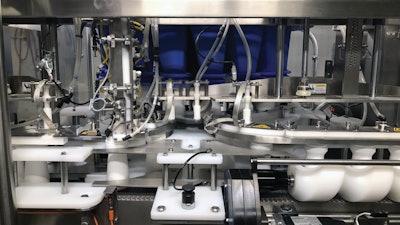
Beech-Nut infant cereal has undergone a packaging transformation driven by consumer needs. Gone is the paperboard carton wielded by moms and dads for generations, and in its place is a sleek co-extrusion blow molded newcomer whose two key benefits are listed prominently on the front of its full-body shrink sleeve label: easy-pour spout & measuring cap.
“Parents are very focused on measuring the amount they’re giving their baby, and that was a package feature not found in the category,” says Andy Dahlen, Vice President of Marketing at Beech-Nut. “So we set out to create a package that would provide that first-in-category benefit.” Also designed into the threaded injection-molded polypropylene closure is a spout that makes it easier to control product flow during dispensing. Dahlen sums up the relaunch this way: “Measurability, pourability, and portability—those were the drivers.”
First shipments of the new container, which holds the same 8 oz. as its paperboard predecessor, started reaching stores in February, and now the container is available nationwide. Secondary packaging, done on three pieces of equipment supplied by Delkor, is notable, too. But we begin with the primary pack.
The container itself, coextrusion blow molded by Silgan Plastics, weighs 43 g. A layer of EVOH serves as oxygen barrier, as some of the products can have their shelf life shortened if residual oxygen levels are not kept low. The other components of the package are
• an induction-sealed foil closure supplied by Constantia
• a threaded closure with dispensing feature injection molded of polypropylene by Mold-Rite Plastics
• an injection-molded PP snap-fit overcap that goes over the threaded closure and doubles as a measuring cup, supplied by Silgan
• a full-body shrink-sleeve label supplied by Hammer Packaging
When asked about the relative cost of the new package, Dahlen says it costs more than the previous package. He adds that the consumer pays a slight premium, too, “though relative to the competition we’re nearly at parity.”
All new packaging equipment
Predictably enough, a whole new packaging line was required for the new package, and it’s an impressive assembly of equipment to say the least. It begins with a Busse depalletizer from Arrowhead Systems that feeds containers into the Morrison infeed timing screw of a Spee-Dee Packaging Machinery continuous-motion auger filler. This machine has 18 pockets on its turret, and each container occupies one of these pockets. So as the turret rotates, the containers pass beneath two dispensing spouts fed by multiple augers. The rotational speed of the turret combined with the RPM of the auger delivers the requisite 8 oz. of product into each container. The filler is rated to run at 100/min.
According to Spee-Dee Vice President of Sales and Marketing Timm Johnson, because the cereal itself is quite fragile, some of the tooling had to be modified so that the product could be handled more gently. Another piece of customization involved the vibration used to settle products whose densities are quite dissimilar.
“A typical rice cereal has a density considerably lighter than an oatmeal-based cereal,” says Johnson. “So the design of the machine permits the operator at the control panel to pick from a menu of different vibration set points depending on the product. In addition, there’s even some variation within a single product being run. So we included one of our checkweighers at the discharge of the filler that provides continuous feedback to the filler. This lets us automatically vary the RPM of the auger—and consequently the amount of product being discharged with each cycle—based on that feedback.” Facilitating all of this machine-to-machine communication is the fact that the Spee-Dee checkweigher is controlled by the same Rockwell PLC that controls the Spee-Dee servo-driven auger filler.
Chris Darling, Director of Engineering at Beech-Nut, adds that ease of cleaning was another driver in making the Spee-Dee filler such a good fit in the new line. “The other big thing that we were after was that we had an extremely aggressive timeline as the new container was developed,” says Darling. “So when it came to picking a filling machinery supplier, we wanted partners with experience handling similar products. Spee-Dee was not only a good partner for us but had many partnership relationships with the other machinery suppliers whose components are integrated with the actual filler itself, which helped streamline the process.”
There are three important pieces of equipment integrated with the filler. One is the Fords aluminum closure press. This machine punches skirted foil closures from roll-fed aluminum and sends them through a chute that leads to the discharge starwheel of the Spee-Dee filler. So as each filled container exits the filler, it receives a skirted foil closure.
The other equipment integrated with the filler is the R.A. Jones MAP Systems gas flushing system. Just before containers enter the filler, a MAP Systems overhead gas rail nitrogen flushing system drives out ambient air. This overhead gas flushing continues as containers move through the filler and then through a Fords Linear Belt Sealer. This machine uses a top belt to apply pressure on the foil cap as it passes an induction field, securing the foil cap to the container. The induction field is generated by an Enercon induction unit that is fully integrated into and controlled by the Fords machine.
Ink jet and capping
Shortly after the Spee-Dee checkweigher, a Markem-Imaje ink-jet printer puts lot and date code on the bottom of each container. Next comes a pair of Arol rotary cappers each with eight stations. The first applies the threaded dispensing closure and torques it down while the second snaps on the overcap/measuring cup. “We chose Arol because of their depth of experience with this kind of application and they offered the monoblock configuration we wanted,” says Darling.
Next in line is the application of the full-body shrink-sleeve label on an applicator and shrink tunnel supplied by American Fuji Seal Inc. Made of PETG, the label is printed flexo in 10 colors by label converter Hammer Packaging.
At this point it’s on to secondary packaging, executed by three pieces of equipment from Delkor Systems. First a Trayfecta S Series erects corrugated trays from flat blanks and accumulates them side by side on a feed conveyor leading into the Delkor Flex Loader’s flighted conveyor, which runs parallel to the conveyor on which filled containers are conveyed. A servo cross-push mechanism sends two trays at a time off at a right angle and into the flights of the Flex Loader’s transport conveyor. A gantry pick-and-place device with a dual split head end effector mechanically picks 12 containers and fills four three-count trays per cycle.
Once the trays are loaded with canisters, trays are then fed into a shrink bundler where the two display trays become a single shipping package. Between the Flex Loader and shrink bundler is an integrated top-pad placer. For many packages, this top pad is critical to unitize the two (or more) trays together as a stable shipping unit. This is a patented Delkor package solution called the Turbo Case, and it was a key factor in Beech-Nut’s decision to choose Delkor for the secondary packaging solution. The machine also has the capability to do Spot-pak in the future.
“It’s really an ideal on-shelf format,” says Darling. “Store personnel can quickly remove the shrink wrap and place the trays on the shelf or they can remove canisters and place individual units on the shelf. Sustainability was also a factor in our selection as the secondary package provides us with a reduction in corrugated vs the original package that was in a full wraparound case.” The final step of the process ends with another Markem-Imaje Case Coder.
Palletizing is currently done manually. “Automatic palletizing will be looked at in the future,” says Darling.
To view a video of the auger filler, go to pwgo.to/3105.