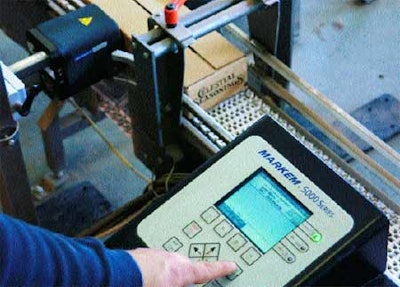
It’s said that patience is a virtue. It’s also a quality possessed by those with a long-term outlook, like managers at tea packager Celestial Seasonings, part of The Hain Celestial Group.
Managers knew for years they needed to change from contact coders to some other type of coding system to mark cases with information at the company’s headquarters plant in Boulder, CO. Yet they weren’t sure what technology to invest in. They’d used several types ofcoders; contact coders had issues of inflexibility, messiness, safety, and slower speeds, while print-and-apply systems meant higher costs for labor and supplies and ate up valuable storage space, managers say. During visits to nearby installations, they also found that mid-1990s ink-jet units were problematic.
Thus, the company waited several years before procuring the coders they knew would fit their requirements to a T: Markem (www.markem.com) Model 5200 dual-head large character ink-jet coders.
“Several factors came together for us,” explains senior director of operations David Ziegert. “More and more customers asked for bar codes as our business grew to a ‘critical mass’ where the labor-intensive off-line print-and-apply operation became impractical.
“We also found that Markem’s resin-based TouchDry® ink provided the print quality we needed to be able to code every case of tea within our facility at a reasonable cost. Our cases are distributed throughout the United States and globally, and the bar codes must be readable in warehouses from Philadelphia to the Far East.” TouchDry is a solvent-free hot-melt ink supplied in solid form.
The commitment to the Markem 5200s followed a three-monthtest run of a single unit. That success lead to a series of installations starting in 2002. After the most recent coder was installed, in fall 2004, the plant had seven Model 5200 coders printing on two sides of corrugated cases containing cartons of tea bags. The coders are located at the discharge end of case packers scattered throughout the plant. They print onto five different sizes of cases containing 6, 10 or 12 cartons to total some 275 different products with a wide range of production rates, Ziegert says.
Ziegert says the company’s environmental stance compels it to use corrugated with high recycled content. Corrugated inconsistencies related to ink bleed had been an issue with the contact coders.
“Recycled content cases tend to be darker, which is a challenge to get good contrast with bar codes,” offers production inventory manager Robert Fleming.
Two major benefits are the functionality and fool-proof nature of the units’ easy-to use keypad operator interface, Ziegert emphasizes.
That’s crucial in an operation where changeovers rule the day. Before, the contact coders required new coding to be manually set any time the shift, day, or product changed. Now, rollover of day and shift is automatic, and any other changes can be made via a keypad.
“Issues with the wrong alphanumeric coding or improper bar code have been significantly reduced with these units,” says Ziegert. They also like the exactness of time stamping, a crucial feature that the contact coders lacked.
Coders’ changeovers took from five to 15 minutes, depending on the operator, with the previous contact coders. Now, “changeovers are as easy as pushing a button,” says Fleming. He also appreciates the template-based software program, Markem’s Composer™. Composer provides WISYWIG interface, EAN 128 bar code assistance, and graphics support for popular formats. “Operators interface with a database so that any product can be printed on any line. We can print logos if we want, too,” Fleming adds. That’s going to get even easier. By the time this article appears, the company will have networked its printers, which permits simultaneous changes or changeover of one unit from any of them. At the same time, the company is installing bar-code scanners supplied by Markem that will be mounted after the coders. “This will provide some interesting information like case counts,” says Fleming. “It will also permit us to access all of the coders at the same time such as for firmware upgrades.”
Simple benefits
Manufacturing manager Art Osborne says standardization to one model of coder simplifies things. “It eliminates the complexities for mechanics, and spare parts are interchangeable. Maintenance for the coders is very simple, and mainly involves changing a filter every six months. The units clean up easily, and the ink is easy to work with. Plus Markem has 24-hour technical support, which gives off-shift crews troubleshooting assistance.” The plant operates 24/5.
Planning analyst Mike Crowe arrived after the ink-jet coders were installed, but even he appreciates their reliability the year he has been with the company: “They run daily for 24 hours, so it’s impressive the few incidents of problems we’ve had either mechanically or with the print quality.”
The addition of the ink-jet coders “also permits our flexible labor force to be doing other things,” Ziegert says. “With the Markems, coding is no longer a limiting factor to helping us achieve our goals.” The company pegs a one-year payback for each coder.
“Our process expansions from now on will include a Markem coder,” concludes Ziegert. That’s the confidence that comes from a patient, long-term perspective.