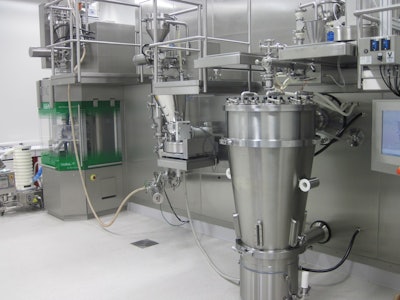
AstraZeneca is a pioneer in the development of continuous processing of solid dosage forms (tablets). To further strengthen its clinical trial manufacturing capability in Mölndal, Sweden, AstraZeneca has recently invested in a continuous wet granulation unit, ConsiGma™25, from GEA Pharma Systems.
The wet granulation unit will be used for the development of novel drugs and also to produce materials for clinical trials. AstraZeneca develops novel formulations and manufactures materials for global clinical trials in its R&D facility in Mölndal. Larger-scale production is transferred to AstraZeneca’s commercial production facilities.
GEA Pharma Systems’ technologies are based on granulating, drying, and making tablets using potent APIs. The concept of converting traditional batch production into continuous processing has been developed further over the last decade and is now rapidly gaining interest.
”We are very pleased that AstraZeneca selected GEA Pharma Systems’ technology and drives the development within the industry in general towards continuous production," says Daniel Frosterud, Sales Manager of Christian Berner, agent for GEA Pharma Systems in Sweden. “There has been a longstanding relationship between AstraZeneca and GEA Pharma Systems for batch granulation technology, and the continuation—with its third purchase of continuous granulation technology—strengthens further this relationship,” adds Michael Van den Bossche, Sales Manager of GEA Pharma Systems.
The ConsiGma can produce granules continuously, there is no waste during startup and shutdown, and the batch size is determined simply by how long the machine is run. It also provides benefits in the development of new products as process parameters can be changed easily during experiments, resulting in shorter development time with less material used. Critical quality attributes are measured throughout the process.
ConsiGma was developed in compliance with the U.S. Food and Drug Administration’s QbD initiative. It satisfies the industry’s need for reduced risk and higher quality while avoiding lengthy and costly validation and scale-up to bring products to market faster. This flexibility enables the production of products to meet demand, keep expensive cleanroom space to a minimum, and reduce inventory costs. Integrated advanced process control and PAT tools allows monitoring during production, so quality can be designed into products from the start.