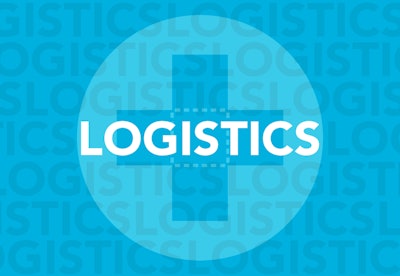
Many doses destined for clinical trials end up being thrown away because a flawed logistics process results in temperature exposure beyond stability limits. Inadequate attention to logistics can also skew trial results, particularly for fragile biologics, which can be rendered ineffective if exposed to too much vibration.
Paying attention to logistics from the beginning of the development process is key to minimizing waste, protecting product efficacy and launching as quickly as possible, according to Steven Jacobs, MBA, R.Ph, president of Global BioPharm Solutions, a consulting firm based in Hatfield, Pa. In an interactive workshop, Overcoming Logistical Challenges for Global Trials, on the opening day of the BioLogistics Summit (June 27-29, 2016, in San Francisco), Jacobs noted timely completion of successful trials also maximizes return on investment. “Every delay reduces the revenue a new drug generates,” he explained.
“Logistics needs to be involved from the beginning and at each step,” he said. A successful trial depends on considering logistics at manufacturing and blinding, comparator sourcing, labeling and packaging, storage and distribution, clinical sites, and returns and reconciliation.
Early and ongoing collaboration and thorough logistics planning prevent shipment-delaying supply chain surprises like incomplete customs documents or an overlooked risk (transit strike, bad weather, natural disaster, deviation from tested transportation route). Good planning and collaboration also decrease spikes and troughs in demand and allow time for comparator sourcing and regulatory filings.
In addition, Jacobs stresses the importance of well-written, illustrated standard operating procedures, which not only explain how to do a task, but why it’s done. “There’s a growing interest in risk-based quality. You need to be able to show you have control of your process and that it works the same way each time,” he said.
Jacobs also recommends clinical trial organizers:
- Make good communication with all stakeholders an ongoing priority
- Run as many process steps in parallel as possible (e.g., packaging and labeling)
- Select countries where trial materials will be shipped and understand national requirements for shipment approval, expiry dating, customs documents, depot handling and other variables
- Identify each touch point from manufacturer to each investigator site (touch points pose highest risks)
- Determine whether mass shipping or just-in-time works better
- Ship by air, understanding that next flight out (on a commercial flight) may be more cost-effective than standard air freight in the long run
- Understand cultural differences and do due diligence on depot managers
- Standardize on a universal packout to streamline the process and prevent errors
- Select packaging that maintains the product within the required temperature range for 120 hours to minimize chances that a delay will ruin the product
- Consider reusable packaging
- Select shipping dates to avoid potential delays caused by weekends and holidays (for global shipments, be aware of holidays at the destination)
- Select knowledgeable shippers that can prevent problems or solve them quickly to minimize delays
- Pay special attention to label adhesives to ensure adherence, especially if vials will be cold when labeled
- Plan for returns and reconciliation to meet Good Distribution Practices requirements
- Plan for integration of interactive response technology, randomization, electronic patient-reported outcomes and electronic case report forms
- Have quality agreements in place with all departments and suppliers (although it’s not required in the United States, agreements increase FDA’s comfort level with your process)
Finally, Jacobs advises, “Hope for the best and plan for the worst.”