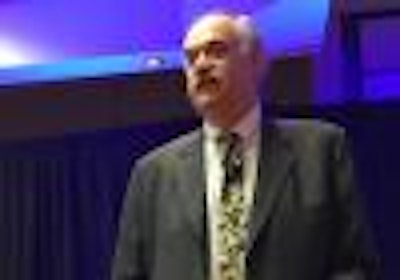
Think about all the ways you spent your leisure time as a kid. How you listened to music, how you watched TV. Maybe you listened to records or threw a tape into your boombox. You had perhaps four channels you watched, and if you missed a show, you missed it. Think about how you communicated with your friends—calling them on the phone or knocking on the door to see if they could play. Today our kids see no need to sit down in front of anything but their phone or computer; no need to plan their time around TV shows. They stream what they want when they want, and they communicate with their friends the same way.
It’s easy to see how the Internet changes everything.
Well, not quite everything. The Internet hasn’t had much effect on discrete manufacturing, which still programs controllers much the same way it did in 1980. It hasn’t had much effect on the power grid, which looks the same as it did 65 years ago. It hasn’t had much effect on aviation, which still downloads jet performance data by hand.
“No, the Internet didn’t change everything. There is still much to be done,” says Richard Soley, executive director for the Industrial Internet Consortium (IIC).
And that’s where organizations like IIC are coming into the picture, trying to create a link between the Internet capabilities we take for granted in our everyday lives and industrial standards that fall considerably behind. “What’s really missing is Internet thinking,” Soley says. “There’s a tremendous gulf between Internet systems and manufacturing systems.”
Soley—detailing the status of the Industrial Internet of Things (IIoT) in a keynote speech at The Automation Conference, hosted by Automation World this week in Chicago—espoused the benefits of industry coming around to that Internet thinking.
The Luddite frame of mind that’s as prevalent in the Internet revolution as it was in the industrial revolution before it is not necessarily a bad thing, Soley said. After all, one of the ways we get efficiency is by doing things the way we’ve always done them. But the social disruption that comes with such revolutions can also translate into huge productivity increases, he added.
Although perspectives differ about specific values for the Internet of Things, the general consensus is that the measurable outcome will be in the trillions of dollars.
None of the technologies involved are particularly new. “The idea of applying that technology to industrial systems, however, is a damn good idea,” Soley said.
For its part, IIC isn’t focused on technologies, but rather on business outcomes. “What we’re looking for is transformational change,” Soley explained. “That is really, really hard, and it’s really about leadership.”
It’s also about testbeds—trying things out, seeing what works, and creating standards around that, rather than creating standards first and hoping they can be applied to real-world situations.
One manufacturing testbed, led by member companies Bosch, Tech Mahindra, Cisco and National Instruments, is focused on track and trace. “If you know where everything is on the factory floor…you can make that factory more efficient and more safe,” Soley noted. The testbed has achieved 1 m location accuracy so far, but expects to soon get down to 3 mm, he added.
National Instruments and Cisco are also working with RTI on another testbed focused on communication and control—specifically, integrating less consistent renewable energies with the power grid. They’re building a test cell now, but will build a larger cell in California if that’s successful. “A lot of the same technologies that work in the manufacturing space are just as important in the power grid space,” Soley said.
Those technologies are also important for other industries, such as healthcare and farming. Soley pointed specifically to the oxygen sensors that are commonplace during surgeries today. They’re a vital piece of equipment that can make a difference between life and death, and yet they have a 20 percent failure rate. Problems could be solved by integrating O2 sensors with respiration sensors, and yet there is zero integration today.
They’re not made by the same manufacturers, and they don’t operate on the same networks—the same problems faced in manufacturing, Soley said. “These are problems we can actually solve.”
Likewise, a John Deere harvester knows a lot more about the farm than most farmers do, Soley said, and knows what will be planted next year. And grocers know exactly what consumers are likely to buy next year. But with no integration between the two, there is considerable waste. “One third of all perishable food in the U.S. perishes en route from farm to table,” Soley said.
“We have to learn how to reduce that,” said Dewey Scott, operations manager and technical director at Scott Farms. The North Carolina-based sweet potato grower and processor is using a cloud-based solution to do just that. “We now can get a handle on the buying patterns of our customers.”
To learn more about the software and serialization solutions Scott Farms has put in place, read “Unique Serialization Comes to Fresh Produce,” which details Dewey Scott’s presentation at The Automation Conference.