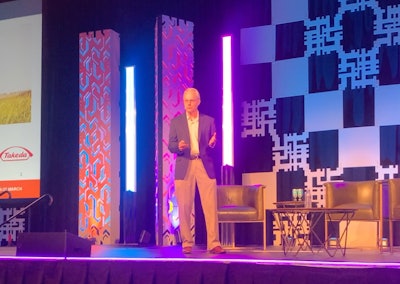
Biopharmaceutical manufacturing will always have challenges, even for products manufactured day in and day out in 24/7 operations. But ultra-rare drug manufacturing comes with its own unique hurdles. If a drug is only produced once every few years, how does a company retain knowledge among staff?
At the PDA Annual Meeting this week, Patrick Gavit, head of manufacturing science at Takeda, offered insights into how their Los Angeles manufacturing facility produces a super-orphaned drug once every five years for infants suffering from infant botulism, which can lead to muscle weakness, trouble breathing, and more.
Takeda produces the drug on a contract basis for the California Department of Public Health (CDPH), who owns the license for this public service, not-for-profit orphan drug. It is filled by Emergent BioSolutions in Baltimore.
As Gavit explained, the drug is colloquially called BabyBIG because it's used to treat infants under one year of age who have infant botulism, and the BIG is an acronym for Botulism Immune Globulin. The drug is purified from human plasma, obtained from volunteer donors who have been inoculated with the botulinum toxin so that they produce antibodies targeted against the toxin.
BabyBIG is the only approved treatment for infant botulism, and there are on average 150 infant patients per year in the U.S. in need of the drug. Because Takeda manufactures one batch every five years, and source plasma comes from only 30 donors, Gavit upholds a “batch right, first time” approach because there is no second chance to get it right.
Gavit offered tips for success in producing ultra-rare drugs, given the infrequent manufacturing schedule.
1. Modern manufacturing suite
The manufacturing suite where BabyBIG is produced is shared with another product which is typically produced 24/7/365. To produce BabyBIG, they need a six-month window that entails moving out the equipment from the other product, moving in the equipment for BabyBIG, doing validation activities, training the operators, doing practice runs, and doing the actual manufacturing run. “There's a lot that is contained in that six-month window. What really enables us to do this well is a very flexible manufacturing suite. All of the equipment—with the exception of a few centrifuges—is mobile, on wheels,” said Gavit.
They wheel out tanks for the other product and wheel in equipment for BabyBIG. “There are three viral zones in the manufacturing suite, and both products need all three of those zones. We also have the ability to adjust the temperature in the rooms from either ambient to 5°C—some of the BabyBIG process needs 5°C, whereas the other product just needs ambient temperature. So having that flexibility is key,” he said.
Gavit explained that they can control temperature on the tanks by wheeling them to a thermal fluid line coming in through the wall. The modern, flexible manufacturing suite was awarded the ISPE Facility of the Year award in 2018.
2. Streamlined changeover and digital mapping
Takeda utilized the Operational Excellence workstream, SMED (single-minute digit exchange of die), to reduce changeover duration from 33 days to 16 days. This encompasses movement of equipment, rebalancing the room, and qualifying the area, and then the remainder of that six-month window is for validation, practice runs, and the actual manufacturing run.
As an aside, the company only uses plasma units above a certain titer in the manufacturing pool. The other units, low titer plasma units, are used for those practice or engineering runs instead of being discarded.
Said Gavit, “We're able to utilize a digital mapping tool called Matterport, which is very helpful because we can virtually move through the rooms and take exact measurements, so we know exactly where we want to put everything. That way you can plan how you want to do this changeover, which equipment you want to move out first, how you want to set up BabyBIG equipment in the zone and in the facility. That was very helpful in terms of reducing the changeover time.”
3. Long range supply chain plan
Because the suite is typically being used for full-time manufacturing of the other drug, they plan their supply chain out 10 years to ensure patients of that drug are not impacted. Gavit noted, “That's basically two BabyBIG campaigns into the future. By doing that, we're able to then plan how we're going to ramp up production of the other product to make sure there's enough so that during the six-month window, we can still supply the global patient needs for that other product.”
4. Knowledge retention
Producing approximately every five years, how does staff remember how to process the drug? “Every time we have to do a campaign, obviously we need strong documentation. We have videos of all the unit operations that we're able to use as the initial training for the new operators, as well as refresh the memory of those operators who have worked on previous campaigns,” Gavit said. “It's also very important for us to retain key SMEs who have worked on previous campaigns. I would say that this product is a source of great pride for our site and for the company, and people are raising their hands wanting to work on this.”
People who have worked on BabyBIG in the past tend to gladly step away from their current roles to work on it again for the six-month period. “There's good support among their managers, among the site leadership in allowing us to have them. The manufacturing operators who produce this are the same operators who produce the other product that's in that same suite,” he explained. “But we also make sure we're bringing on new talent to work on this product so that when the current SMEs move on and are no longer with the company, we've always got a supply or a bench strength of people who know the process.”
5. Maximizing non-GMP space
Much of the equipment testing, training, and optimization can be performed in a non-GMP space before it’s moved into the BabyBIG manufacturing suite.
6. Equipment upgrades
Gavit said they are always looking at upgrading the equipment used in the process, making sure that it's new and reliable: “CDPH has been very good about allowing us to replace some of the equipment… this upcoming campaign in 2025, we have six new process tanks. So that ensures that we always have well-performing equipment and increases our chances of getting this right the first time.”
7. Strong CMO-client relationship
Gavit gave credit to their strong CMO-client relationship, which is actually a three-way collaboration between Takeda and CDPH and Allucent, a contract regulatory firm. “They do all the communication with the FDA. They also manage a lot the program management aspects of the product. So it's a really good collaboration. There's a lot of trust between these three entities. We've been working together for many, many years and I think it helps that this is a not-for-profit product,” he said. “Finally, we have a great partnership with the FDA, and they understand the unique challenges of producing such an ultra-orphan drug. They've been great in working with us to figure out our approach.”
To conclude, Gavit acknowledged some of the entities involved in BabyBIG, including praise for the late Dr. Stephen Arnon: “He's really who you would call the father of BabyBIG. He first recognized infant botulism as a unique disease back in the 1970s, and he began working on this medication at that time. So it's really through his hard work and efforts and interest that BabyBIG has come to fruition. Sadly, he passed away a year and a half ago. Dr. Jessica Khouri has taken over the helm as the lead.” She has been very involved in the BabyBIG program for many years.