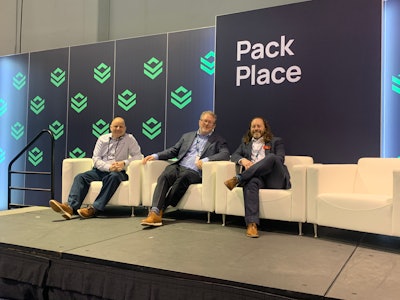
On Sterile Packaging Day 2024 at MD&M West, Henk Blom, Todd McDonald, and Nick Packet discussed a roundup of sterile packaging updates from the FPA’s Sterilization Packaging Manufacturers Council, including their mission, efforts to educate policy makers on sterile packaging to help prevent unintended consequences from well-meaning legislation, and best practices for storing rollstock/pouches for sterile barrier systems (SBSs).
On the latter topic, while many are rightly focused on what happens to the package after filling, rollstock storage considerations prior to packaging are also critical to success. Blom shared common tips from an SPMC white paper, Rollstock Storage and Handling, to protect your materials before packaging.
Rollstock and pouches should be protected from the elements—kept clean and dry—with minimized exposure to direct sunlight. He noted that while it may sound like common sense, not every facility around the globe features a pristine warehouse, with climate and pest control. Dust and chemical contamination, which can be carried into cleanrooms via packaging, should also be minimized.
Rolls are typically individually wrapped on a pallet and should remain packaged until ready for use. In cases where only a partial roll is used, it’s a good idea to keep the outer packaging and re-wrap rolls if they’re returned to inventory for future use.
Storage conditions play an important role in the health of your rollstock. Stock is typically best stored at 50-80 °F (10-27 °C) but Blom said to consult your supplier for material-specific conditions. What happens if rollstock deviates from temperature requirements? Blocking (in which one layer sticks to another), wrinkling, or crushed cores can occur.
Blom noted another temperature consideration: slip agent behavior. “A lot of sealants—such as polyethylene and peelable sealants—are processed with low levels of what’s called a slip agent. This helps the materials move though the equipment. That material is designed to bloom to the surface and give you a low coefficient of friction so that you get good machinability,” he explained. “But as the temperature changes, the solubility of that slip agent in the material changes. As the temperature increases, the slip actually wants to go back into the material. And so your COF [coefficient of friction] will start to increase and the material will start to stick and slip as it's moving through, for instance, a flow wrap machine.”
The good news here is that this process is reversible by placing the roll in cold storage, which will allow the slip to bloom back out to the material’s surface.
While many common packaging materials like oriented PET, foils, highly engineered papers, and various polyolefins are not typically affected by humidity, there are certain nylons and papers that can be affected. Here, it’s important to check with your supplier, because certain papers can absorb and desorb moisture with changes in humidity. The good news, Blom said, is that this is reversible, but it’s preferable to ensure protection from the start.
Nylons can absorb 5 to 9% of their weight in moisture. “That's a significant amount of moisture, and it can change the physical properties quite drastically. If you dry it out completely, it becomes somewhat brittle, and then as it absorbs more moisture, it can become much more stretchy,” Blom said. “In roll form, it can actually start to wrinkle because it also expands the material a bit. Again, this is reversible, so you can put it in a drier environment and that moisture will eventually equilibrate back out.”
The location of the nylon layer matters. “If your nylon is in the middle of a multi-layer, coex structure, it's not actually seeing the ambient humidity, it's protected by the outer layers. So it's not as much of a concern there,” he added. “But if it's the outer layer of the laminate, or the standalone material with a heat seal coating on it, for instance, we generally would wrap that in the metallized polyester to get maximum barrier protection.”
If there’s a big difference between storage and floor conditions, Blom said it’s a good idea to condition your rollstock, allowing 24 to 48 hours for the material to equilibrate to ambient conditions before packaging. “Some materials will be more susceptible than others,” he noted, adding that if COF is an important consideration, then conditioning will help stabilize the material.
Blom hammered home that some materials have unique requirements that may not be covered by the more common storage recommendations he shared. “So, it's important to always work closely with your material supplier to understand if a particular material has any specific storage requirements that need to be taken into consideration,” he said.
View the white paper here. For a list of all SPMC white papers, click here.